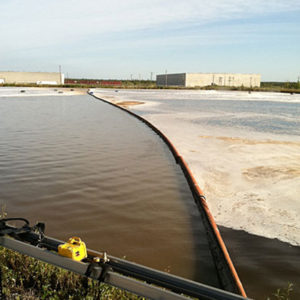
Specified Solutions for Engineers
Architects and engineers require specifications for proven, trusted, time-tested products, where cost and lead-time are critically important. When it comes to wastewater lagoon baffle curtains, we are the architect and contractor trusted advisers, able to offers solutions specific to an application, to help solve problems. Since 1964 we have provided objective answers to help determine the right product for each project. Working with JPS you can expect:
· Secure download area
· Technical specifications
· Importable, high-quality CAD files
· Product descriptions and details
· Case studies for similar applications
· Experts in baffle curtain design for wastewater lagoon
· Proven expertise, expertise, and advice
JPS has pushed the limits of many materials for decades, with one thought in mind – “How can we make a stronger baffle and make it last longer?” Today, JPS Baffles are hand constructed using the strongest nylon scrim available, with rip stops every 5th filament of the material scrim to help prevent tearing. Our anchor system is cast concrete blocks along with a minimum ballast of 5/16-inch galvanized steel chain sewn directly into a special hem in the bottom of each baffle section. Special nylon straps, which maintain a tensile strength between 12,000 lb. and 20,000 lb., are sewn into the sides, tops and bottoms of all sections. All hardware is 304 stainless steel. Definitely ready to take a beating.
All structural components of JPS Baffles are manufactured using nylon materials to maintain a uniform rate of linear expansion which helps to eliminate friction. Stress is evenly absorbed throughout the structure; a claim no other manufacturer can make. This is largely due to the construction techniques utilized when building each baffle section. For example, strength and flexibility is added to seams and hems by sewing them together using silicone-treated nylon thread and reinforcing specific areas as recommended by the hydrodynamic model. It is this careful attention to detail and uniformity that insures JPS Baffle Curtains will have minimal wear and tear and a long life in each application.
For generations, JPS has worked to provide a complete solution. From plotting the exact contour of the basin of a lagoon to provide an exact fit, to engineering treatment efficiencies and recommending the layout of all components, to fabricating and manufacturing the baffle curtains to a precise fit – JPS pulls it all together with our turnkey installation. It is why JPS offers a full two-year warranty which can be extended to five years. We don’t just sell baffle curtains; we engineer solutions that have helped JPS maintain 99% customer retention and satisfaction.
JPS products are engineered systems, custom-designed and precision-manufactured – specific to each application and environment. Installed in the most demanding municipal and industrial processes, many JPS Baffles and other products continue in service more than 20 years later. Industries served by JPS include: Pulp and paper, food processing, chemical manufacturing, oil storage and transport, power generation and more along with many municipal installations.
Why JPS Baffle Curtains are Different
Given the opportunity water will take the path of least resistance, this can result in short circuiting, dead zones, sludge build up and inefficient treatment. Implementing a baffle system to engineer a specific water flow pattern can optimize treatment and retention time.
Figure 1b. JPS Erosion Barrier in Combination with JPS Baffle Curtains.
1b. Intentional Flow Pattern The application of two baffles creates a serpentine flow pattern resulting in increased retention time. The baffles also force the water column through the aerators’ sphere of influence. The entire lagoon is now utilized and aerators maximum potential is realized.