The Finest Baffle Curtains in the World!
JPS Baffles are custom built for industrial and municipal applications using the most durable materials and construction techniques available. While both applications are designed to similar specifications, JPS Industrial Baffles are engineered with reinforcing nylon straps to withstand severe and extreme environments. JPS Baffles are known for their durability due to the materials used, craftsmanship and time tested quality built into the design, construction and installation of every JPS Baffle Curtain. We are proud to call them the best baffle curtains in the world!
JPS products are engineered systems, custom-designed and precision-manufactured – specific to each application and environment. Installed in the most demanding municipal and industrial processes, many JPS Baffles and other products continue in service more than 20 years later. Industries served by JPS include: Pulp and paper, food processing, chemical manufacturing, oil storage and transport, power generation and more along with many municipal installations.
JPS has pushed the limits of many materials for decades, with one thought in mind – “How can we make a stronger baffle and make it last longer?” Today, JPS Baffles are hand constructed using the strongest nylon scrim available, with rip stops every 5th filament of the material scrim to help prevent tearing. Our anchor system is cast concrete blocks along with a minimum ballast of 5/16-inch galvanized steel chain sewn directly into a special hem in the bottom of each baffle section. Special nylon straps, which maintain a tensile strength between 12,000 lb. and 20,000 lb., are sewn into the sides, tops and bottoms of all sections. All hardware is 304 stainless steel. Definitely ready to take a beating.
JPS provides service, maintenance and repair of complete lagoon systems, baffle curtains, erosion barriers, surface aerator replacement and repair, clarifier inspection, air laterals, river outfall inspection, screen cleaning and much more. Services can be scheduled during hot or cold shutdowns providing annual maintenance required for treatment system components. JPS is prepared and for emergency service, and as a longstanding member of the ADC, can have a JPS Dive Team on site within 24 hours.
All structural components of JPS Baffles are manufactured using nylon materials to maintain a uniform rate of linear expansion which helps to eliminate friction. Stress is evenly absorbed throughout the structure; a claim no other manufacturer can make. This is largely due to the construction techniques utilized when building each baffle section. For example, strength and flexibility is added to seams and hems by sewing them together using silicone-treated nylon thread and reinforcing specific areas as recommended by the hydrodynamic model. It is this careful attention to detail and uniformity that insures JPS Baffle Curtains will have minimal wear and tear and a long life in each application.
Developing JPS baffles to fit each individual project requires engineering that is specific to each application. Design considerations include seasonal or environment change, historical weather conditions and more. The custom-fit of each JPS baffle curtain is based on field measurements, of the lagoon, by qualified JPS field technicians prior to fabrication and installation
For generations JPS has provided complete wastewater treatment solutions. The process to build the ideal solution begins with a custom-fit based on field measurements of the lagoon by qualified JPS field technitians. JPS techs will recommend placement of all components in order to engineer treatment efficiencies, then fabricate and manufacture the baffle curtains to a precise fit.
Engineered Retention Time
Water will take the path of least resistance resulting in short circuiting, dead zones, sludge build up and inefficient treatment. The JPS Baffle System forces a specific water flow pattern to optimize treatment and retention time.
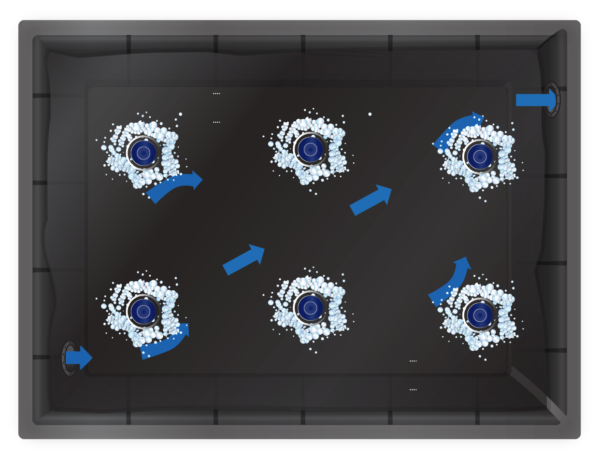
In this example, the water flows directly from the inlet to the outlet of a lagoon in a random flow pattern. Using only an erosion barrier, this results in decreased retention time and reduced BOD removal. The dead zones are not treating waste and the cost to operate these aerators is lost.
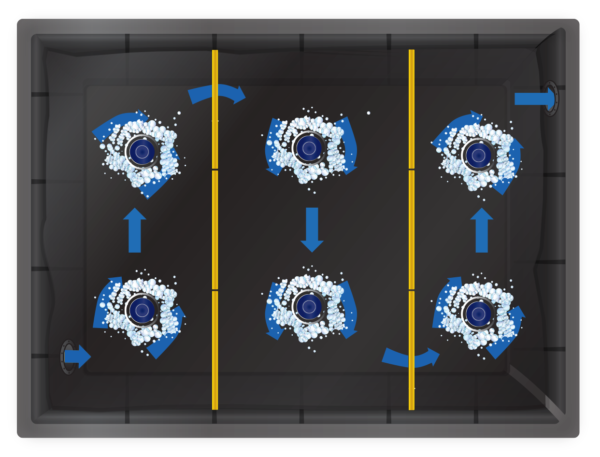
In this example , the erosion barrier is used in combination with JPS Baffle Curtains. The application the baffles create a serpentine flow pattern resulting in increased retention time. The baffles also force the water column through the aerators’ sphere of influence, utilizing the aerators maximum potential.
The JPS Warranty
JPS offers a full two-year warranty which can be extended to five years. Once installed, JPS can be called on for maintenance, review or modifications. We don’t just sell baffle curtains; we engineer solutions that have helped JPS maintain 99% customer retention and satisfaction.